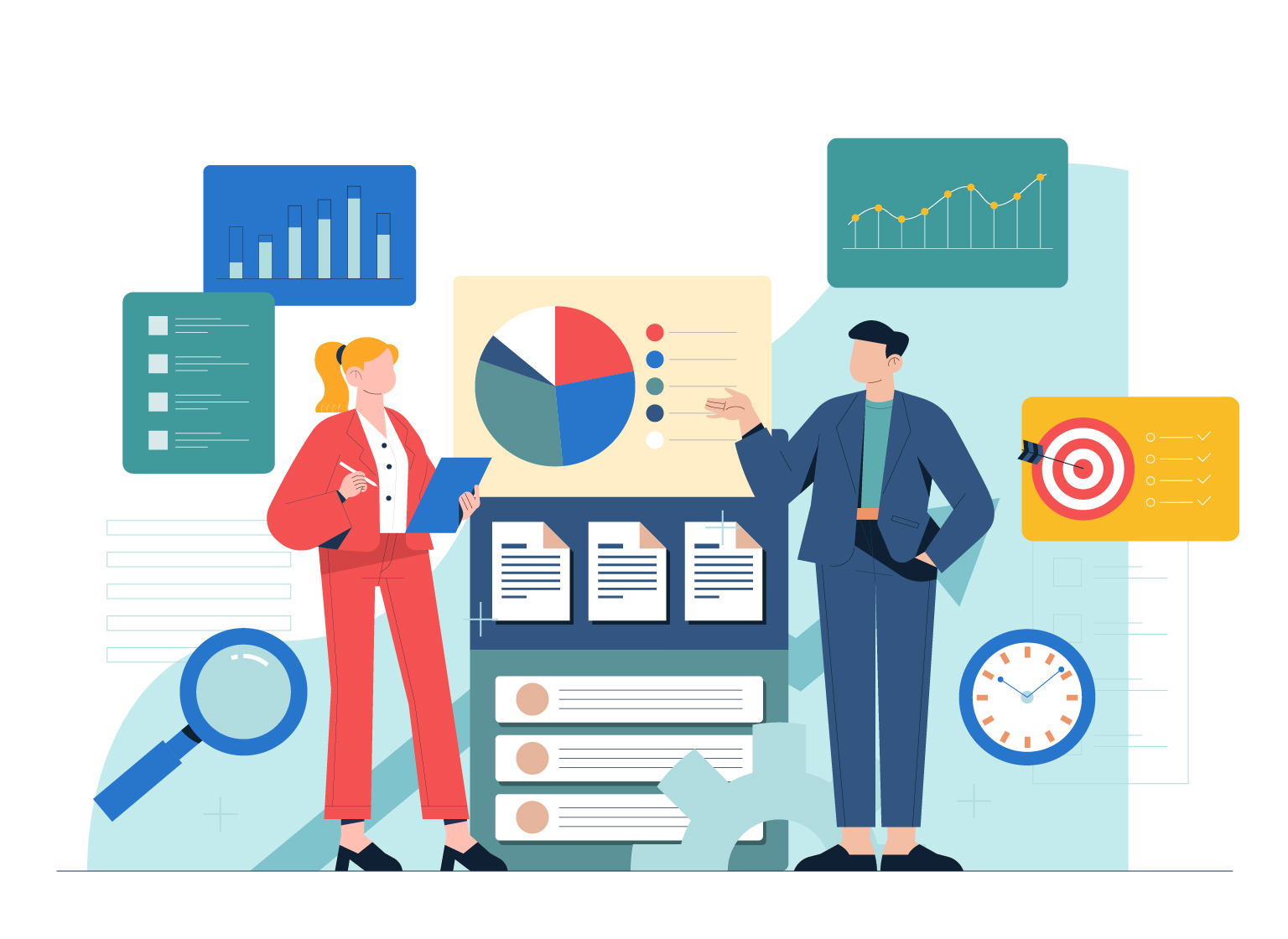
When the world moved to the industrial revolution there arose a process called soldering.
And it was both intentional and unconscious!
Soldering happens when workers slow the operations. During the industrial era, factory workers tried to intentionally reduce their productivity by not achieving their target and sending out a message that this is all they can do.
But there were times this slowing of operations was unconscious. As most factory workers were new and only getting used to the large machinery it slowed their performance.
It is at this stage that Frederick W Taylor tried to resolve the situation with his Theory of Scientific Management.
Scroll down to know how the theory resolves the productivity question.
As a perfectionist, Taylor was not happy with the low performance of the factory workers and thought about what improvements can be brought when the right tool is given to the right employee.
That is how he formulated the Scientific Management Theory or the movement later came to be known as Taylorism
Scientific management is the application of science in management to increase workplace efficiency and staff productivity. By science, we mean using analysis and measurement in the workplace.
Taylor is honored as the Father of Scientific Management as he was one of the initial people who campaigned for adopting science-backed ways to manage people effectively.
Scientific Management research has shown critical approaches to improving workplace culture including improved communication between employees and employers.
The four Principles of Scientific Management Theory include:
The rule of thumb is when something is done according to practical experience rather than theoretical backing. Taylor was of the opinion however small a job it must be done based on scientific knowledge to save human time and energy.
This idea states that the work environment should cultivate harmony between the employee and the employer. Taylor encouraged good interactions that would establish better understanding causing fewer disagreements and more efficiency.
A principle that is an extension of the Harmony, Not Discord principle, here, Taylor stated that both management and workers must understand their mutual obligations. They must work with cooperation and strive to refrain from unnecessary competition.
Taylor encouraged the practice of a scientific approach in the selection of employees. Following such a method helps them understand their physical and mental capabilities thereby providing them the required training to enhance efficiency.
Hence, scientifically approaching work opens a lot of possibilities for the efficiency that the employee and the workspace can achieve.
Let's see what these are.
Scientific management as the name suggests is the application of science in the management of organizations. In his study, Taylor was mainly focusing on workers and ways to improve their efficiency.
Here are some of the contributions of scientific management theory in the workspace.
With many practical applications in the workspace, the theory opens a lot of advantages in business operations. Let's see what they are.
The crux of the scientific management theory is the application of science in improving the efficiency of the workers. A standardization of doing things will help workers to understand the best practices that will get the work done in optimal time.
The greatest revolution of Taylor’s work was that he tried to quantify performance and productivity. For example, by applying the piece rate basis he suggested that the number of work done must be paid rather than the time spent. An employee finishing 10 shirts per day must determine their income than the time they took to finish those 10 shirts.
Taylor was of the opinion that the workforce must be trained in their work than be left on their own to understand what to do. A trained workforce will be fast and efficient in their work as they have a clear idea of what has to be done.
Scientific management encourages better communication between the employee and the employer. Such healthy practices make the workspace better where the management has clarity on the needs of the employees and the employees know how their contribution matters in the business operations.
A scientific and standardized way of doing work ensures optimal utilization of resources with minimal wastage. Scientific management lays the path to such an operation in the workspace, thereby ensuring optimal results through the integration of advanced tools like sales data analytics
But before adopting such a scientifically driven theory into operations, organizations must realize the drawbacks it causes as well.
Scientific management has an extra focus on productivity that it sometimes loses sight of the human factor. For example, by quantifying productivity it falls short in understanding the human factor and puts everyone in a common mold. It does not see each human being as unique and different and emphasizes a standard way of getting things done.
When management focuses solely on the best way of getting work done through management by objectives, it misses the creative and alternative approaches by which the work can be accomplished. Each worker, as an individual, perceives work and the factors around it differently. Expecting all workers to approach the work similarly and anticipating uniform results removes the enjoyable aspect of the job, rendering it dull and repetitive.
When all employees are expected to work in a standard way following uniform rhythm and movement, it eventually discourages workers from initiating any new or creative input. This passive involvement makes the job dull and monotonous, only leading to a decrease in interest and performance.
When employees are always told what to do and encouraged to follow a standard scientific way of doing things, it puts their creative and intellectual approach to work at stake. It is the personal touch that workers bring to the work that makes the job at hand interesting and fun for them.
Despite the drawbacks, the birth of the Scientific Management Theory was a necessity of the times. When the work culture was moving from a small-scale business to mechanized factory jobs, a system had to come that would help both the employer and employee traverse through the new workplace.
When it comes to maximizing productivity and efficiency, scientific management offers a set of strategic techniques that have stood the test of time.
From how tasks are divided and standardized to the way employees are selected, trained, and motivated, scientific management offers a comprehensive framework to boost performance and ensure success. Let’s dive into some of the key strategies:
Standardization is about creating a consistent way of doing things to ensure quality and efficiency. In the workplace, standardizing processes means that everyone follows the same steps, which minimizes errors and ensures that the output is consistent.
Think of this as matching the right person to the right job and then giving them the tools to succeed. Instead of just hiring anyone and hoping for the best, scientific management focuses on selecting workers based on their abilities and then providing targeted training.
Division of labor is all about breaking down tasks so that each worker focuses on a specific part of the process. Imagine a car assembly line—one person installs the engine, another handles the wheels, and so on. By dividing tasks, workers become specialists in their roles, which increases speed and efficiency.
Incentive-based compensation is like giving someone a bonus for hitting a home run. It's a way to motivate workers by tying their pay directly to their performance. If they meet or exceed their targets, they get rewarded, like earning extra cash or bonuses.
Close supervision is about keeping an eye on the work to ensure it's done correctly. In the workplace, this means managers regularly check in on workers, offering feedback and making sure everything is running smoothly. While it might sound intense, this method helps catch mistakes early and keeps everyone on track toward the goal.
Using the right tools and equipment is like having the best gear for a job. In scientific management, there's a strong emphasis on making sure workers have the tools they need to work efficiently and effectively. It's like giving a chef sharp knives or a carpenter the best saw, when workers have the right equipment, they can do their jobs better and faster.
Workplace layout optimization is all about arranging the work environment to maximize efficiency. Think of it like organizing your kitchen so that everything you need is within easy reach. In a factory or office, this means setting up the workspace so that workers can move smoothly between tasks, reduce unnecessary steps, and avoid bottlenecks.
Scientific management might sound like something straight out of a textbook, but its principles are at work all around us, often without us even realizing it. Here are some real-world examples where this theory has been put into action:
Think about how cars are made. On an assembly line, each worker focuses on a specific task—one person installs the doors, another handles the engine, and so on. This division of labor, a core concept of scientific management, allows for faster production because everyone becomes an expert at their part of the process.
Ever noticed how your burger at a fast-food joint is always prepared the same way, no matter where you go? That’s standardization in action. These restaurants can deliver a quick, reliable product every time by creating a consistent process—down to the exact amount of ketchup on the bun.
In a call center, workers are often trained to handle specific types of customer inquiries, making them experts in that area. This is another application of the division of labor. Additionally, call centers often use incentive-based compensation, rewarding employees for resolving issues quickly or making a certain number of calls.
Retail chains often optimize their store layouts to guide customers through a specific path, encouraging more purchases along the way. This is an example of workplace layout optimization, a principle of scientific management. By strategically placing high-demand items at the back of the store and impulse buys near the checkout, these stores increase sales and create a more efficient shopping experience.
Even in the tech world, scientific management has a place. Software companies often use tools to track the time and efficiency of their developers, helping to identify bottlenecks in the coding process. They might also standardize coding practices to ensure that every developer is writing code in the same way, which makes it easier to maintain and update software later on.
In modern workplaces, this theory still shows up in the form of specialized roles, streamlined processes, and performance metrics. While it's great for productivity, it can sometimes lead to a rigid work environment where creativity and employee well-being take a backseat. Today, companies are trying to balance Taylor's efficiency-driven approach with a more flexible and human-centric work culture, recognizing that people aren't just cogs in a machine but valuable contributors with unique skills and needs.
Scientific Management, developed by Frederick Taylor, is like the original playbook for maximizing quality and efficiency in the workplace. The idea is simple: by analyzing every step of a task, you can find the best way to do it, saving time and resources. This approach ensures that work is done consistently and to a high standard, as everyone follows the same optimized procedures. In modern settings, this might look like using data to refine processes or setting clear performance benchmarks. While it’s great for maintaining high-quality output and efficiency, it’s important to keep in mind that flexibility and creativity are also key in today’s dynamic work environments.
From a worker's perspective today, Scientific Management can have both upsides and downsides. On the positive side, it provides clear guidelines and structured processes, which can make tasks easier to manage and reduce uncertainty in daily work. This clarity can lead to increased productivity and a sense of accomplishment when tasks are completed efficiently. However, some workers might still find the emphasis on efficiency and repetitive tasks limiting.
The focus on process can sometimes overshadow opportunities for creativity and personal growth, leading to a desire for more autonomy and recognition. While the principles of Scientific Management can streamline operations, balancing them with opportunities for innovation and personal development is key to keeping workers engaged and fulfilled in their roles.
Irrespective of industries, manufacturing, pharmaceuticals or retail, Taylor’s scientific management remains the foundation of all later productivity enhancement techniques. As the world moved from the mechanical to the digital world, quantifying performance has also taken a huge leap.
Kennect’s sales performance management helps organizations keep track of employee performance for improved productivity and operations. To know more, Book a demo today.
Your data is in safe hands. Check out our Privacy policy for more info